article
The Volkstheater in Vienna
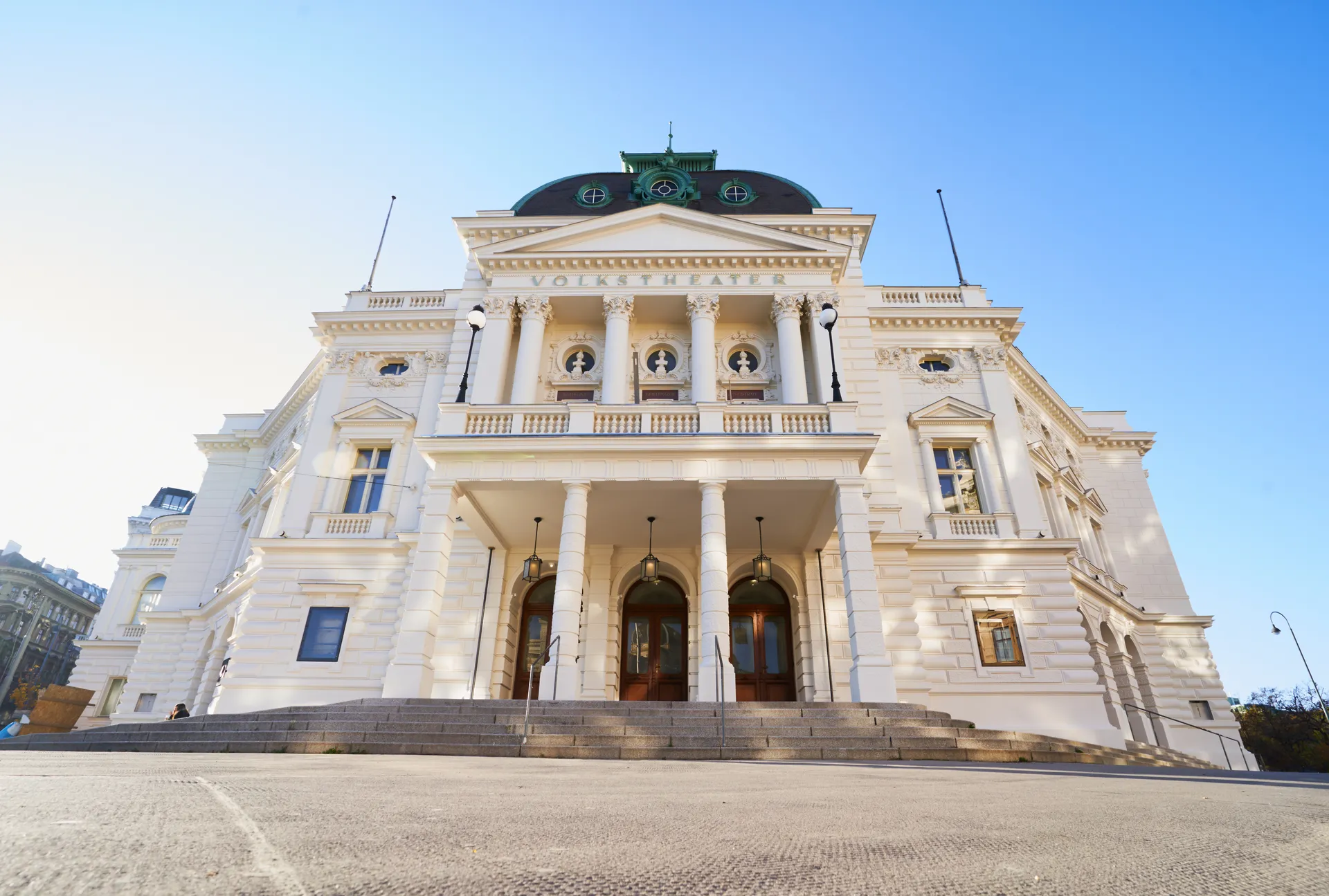
Fotoname: CH-AT-01 (siehe one Drive), ©Evolving Picture
At the time of the Volkstheater’s founding in 1889, the Viennese theatre landscape is still stringently separated by status: The Burgtheater, for example, is reserved for the high aristocracy as an imperial private theatre. More and more voices, however, are calling for a German Volkstheater (People’s Theatre) as a decidedly bourgeois counterpart to the theatre of the court, also in terms of popular education. In addition to folk plays, mainly classic and modern dramas are in demand.
Reading time: 9 Min 1 sec
The “Deutsches Volkstheater in Wien” Association is called into being. Its members include the playwright Ludwig Anzengruber and the furniture manufacturer Franz Thonet. The architects Ferdinand Fellner and Hermann Helmer are also two of the founding fathers of the association.
The Volkstheater in the Weghuberpark is the first building to be erected in accordance with the specifications of the 1882 Theatre Act. It is the first theatre to be exclusively lit using electricity. Together with the architects Fellner and Helmer, Waagner-Biro developed the first fire protection measures for theatres. The fire at the Ringtheater in Vienna in 1881, and numerous other devastating theatre fires in Europe had ultimately given rise to the new safety regulations in Vienna. The research conducted at the time by Waagner-Biro forms the basis for the safety regulations laid down for theatres since 1991.
In order to reach broad sections of the population, the historical founding association already focussed not only on an appropriate programme, but also on the layout of the theatre, which was primarily intended to offer many seats at affordable prices in its large auditorium with very few loges. Over the course of the years, the number of seats was repeatedly reduced in order to increase and improve the view, the level of comfort and the acoustics.
The last significant renovation was undertaken, when the stage technology systems at the Volkstheater in Vienna were upgraded at the beginning of the 1980s.
Since then, the theatre has been transformed from purely ‘en-suite’ operation to an establishment focusing mainly on repertory and guest performances. At the same time, the demands on both technical and economic operations continue to develop. In order to take this into account, the house has recently undergone a comprehensive renovation.
Our colleague, Erich Raser, worked on the 1980s renovation, and was responsible for the more recent modernization in the year 2020.
You started working for Waagner-Biro over 40 years ago. How did that come about?
In 1977, when I was 19, I did a vacation internship in the field of stage technology. My first task was to participate in the Festspielhaus Bregenz project. I finally started working at Waagner-Biro in 1978 after graduating from an higher technical college. My second project was the Volkstheater, where I participated from the very first minute.
What were your tasks in the Volkstheater project?
At the time, the stage technology team was very small with only about 8 people. It wasn’t even a separate division but just a sector of the Mechanical Engineering department.
I acted as the right-hand man of the project manager. From the start, the project manager had me accompany him to all meetings and appointments. It was a very exciting time as I was always involved in the proceedings, from the initial drafts right through to the final construction and commissioning. This was extremely instructive and helpful, not least for the current renovation.
At that time, there weren’t any computers yet and everything had to be drawn by hand. Can you describe to us how such a plan was created?
At first, we drew on drawing boards with pencils or ink on transparent paper. We had a large reproduction department responsible for duplicating the plans. The blueprints for each plan were produced individually by hand.
Before starting to draw, it was necessary to pre-visualise the entire concept. Before I took the pencil in my hand, the plan was already finished in my head. You couldn’t just start drawing and, if something didn’t work, just delete it or push it to one side. Once you’d drawn it, there it was on paper. The parts lists were written manually, and we had to calculate the weights using a pocket calculator.
There were no CAD programmes or anything like that. Our first computers were bought in the 1990s. We even worked in shifts on the first CAD system so that the device could be used around the clock – that’s how expensive it was. There was a CAD workplace in the middle of the office, around which we hung black curtains. Because the quality of the screens wasn’t particularly well-developed yet, it was necessary to do this so that you could discern objects on them properly. Of course, some employees put up resistance to this “newfangled stuff”. In that respect, I started work in the Stone Age of CAD technology.
For the current rebuild, we relied in part on old plans from the archive, which we remodelled in 3D wherever something new had to be added to the existing construction. This was the case, for example, on the grid deck and the galleries, where we installed new drives and stairs.
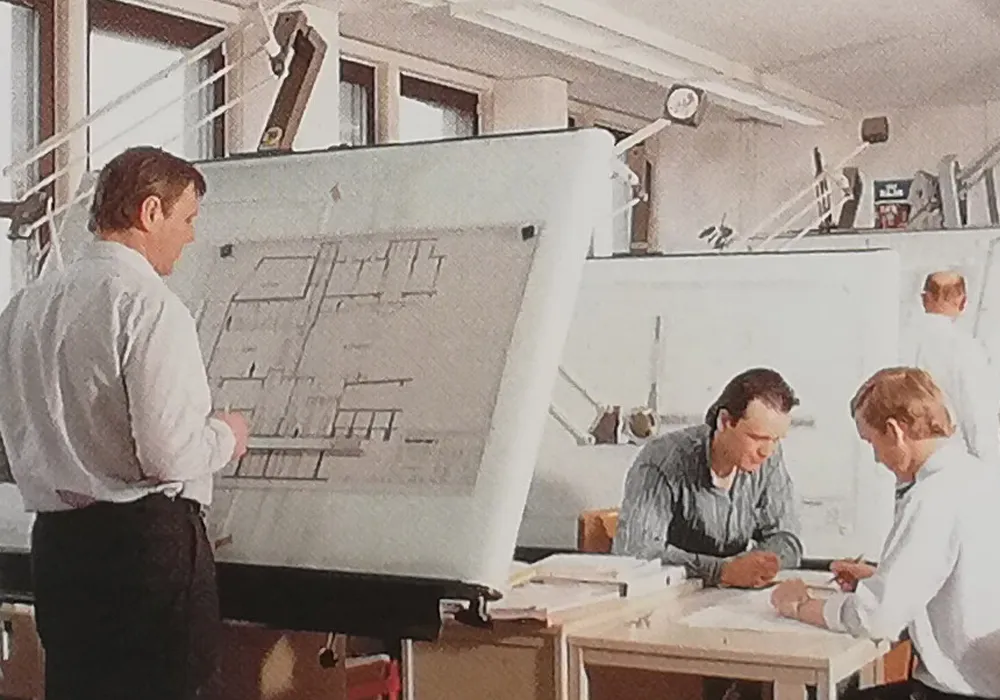
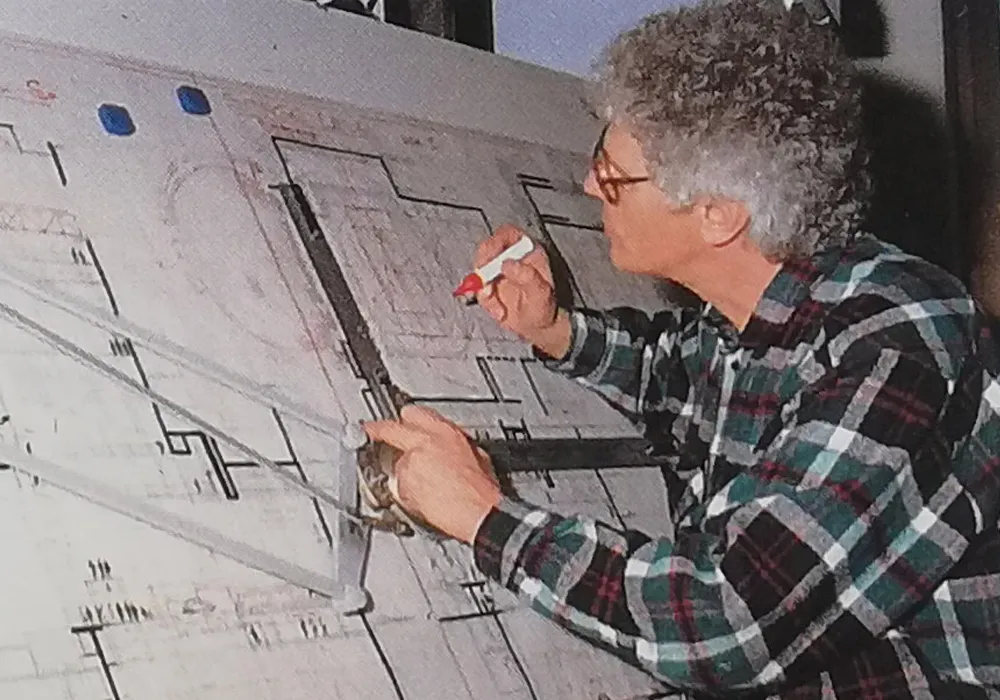
In the beginning, we drew on drawing boards with pencils
The renovation over 40 years ago
What renovations were carried out at the Volkstheater in the 1980s? What was renewed at that time?
It all started with a request for a repair. This gradually developed into a major renovation. At the time, the Volkstheater was completely untouched: Few changes had been made to the original condition of the theatre from 1887, and a lot of it was still made of wood.
For example, objects were brought onstage from the Museumsstraße, where a steep ramp led up from the street onto the stage 3 m above. Scenery was transported by hand from the street onto the stages. This was extremely strenuous.
The payloads in the building were extremely limited. If you look at the roof dome construction from the grid deck, you can see how delicate it is. This is still the original roof construction. The stage technology was actually fastened to this construction – and as you can imagine, it wasn’t possible to place much load on it. The theatre walls, too, were unable to bear loads. This represented the biggest challenge.
For this reason, we installed a steel construction within the theatre which extended right down into the cellar. It had the appearance of a gigantic table on four legs, and all the new stage technology was built on it. This construction is still installed today and represents the basis for the entire stage machinery. During the current rebuild, only the steel support foundations were reinforced, as the required loads had increased again.
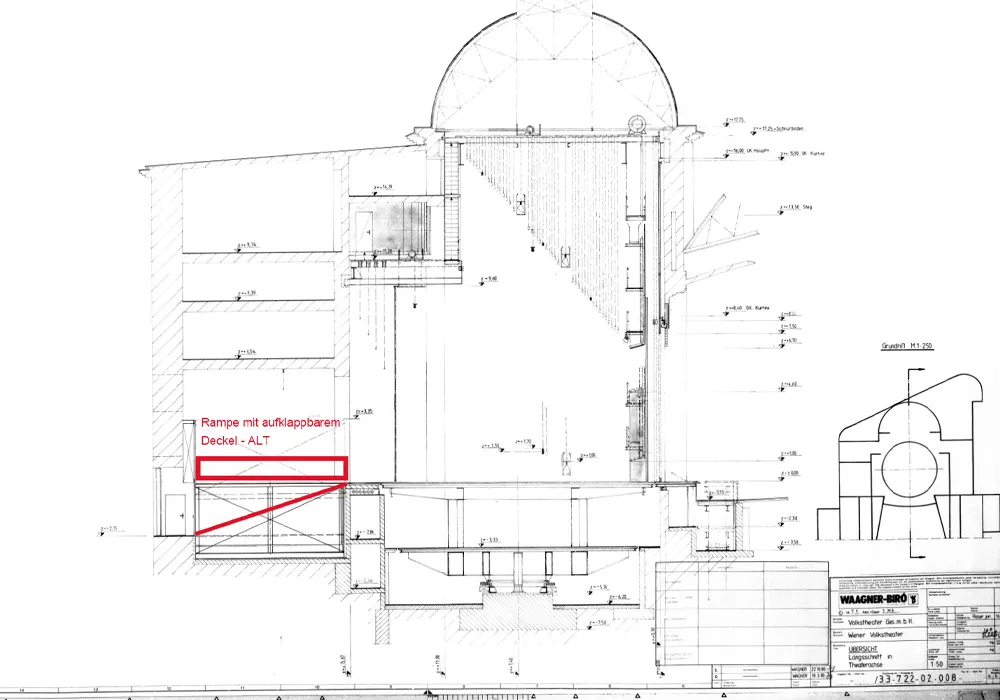
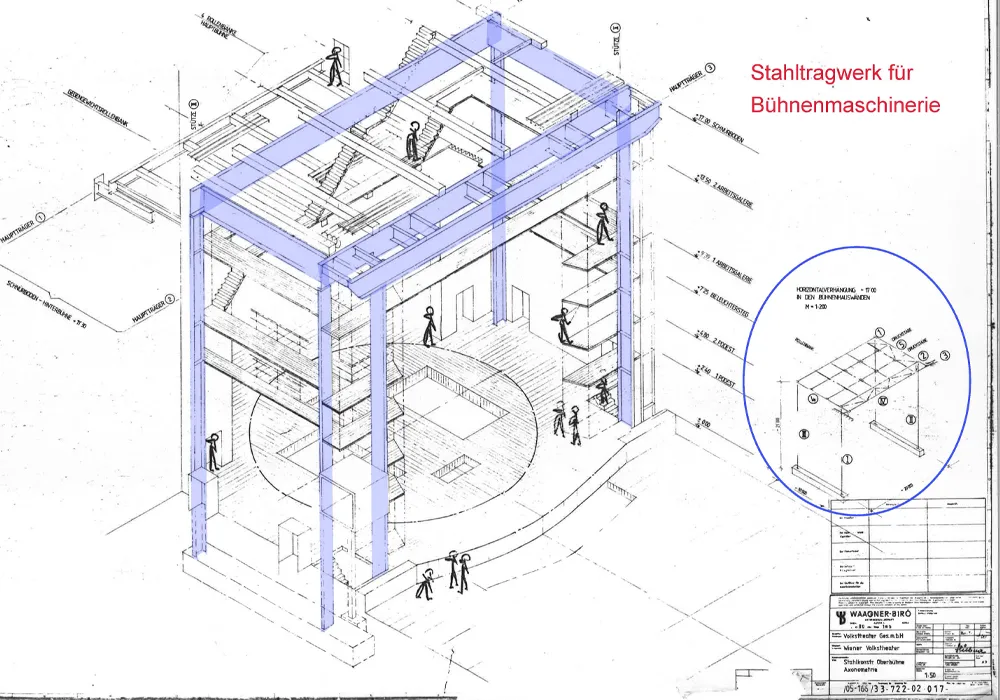
Objects were brought onstage from the road via a steep ramp onto the stage 3 m above it (links) Steel construction installation as reinforcement for the stage technology (rechts)
It wasn't just the upper machinery that was modernised. The lower machinery also received an outstanding innovation for the time.
Yes, that’s true. At the time, the control technology for controllable drives was still in its infancy, and upper machinery with manually operated flybars was installed. There were only electrical lighting hoists, some heavy load hoists, one curtain and one veil curtain hoist – the rest of the upper machinery was operated by hand using counterweights.
But the highlight of the renovation in the 1980s was the revolving stage. In the original theatre, there was just a wooden revolving stage – operated by hand – which rolled on steel balls approx. 5 cm in size. In 1981, we installed a proper cylindrical revolving stage with a central bearing and two trap elevators. The lower stage still works perfectly and was left almost untouched during the current renovation.
The 2020 renovation
What does it mean to you, to be involved in this next renovation after over 40 years?
It has been really exciting and interesting to see all the old stage machinery again, and it is astonishing how quickly you remember all the details. I was involved in the 1980s project from the start, and this was a real benefit now, especially during my talks with the local building supervisor and the planners. Because I had already participated in the construction of the stage technology over 40 years ago, I had all the required background information.
So, what are the new features in the current rebuild?
Grid decks
Until 1980, the grid deck in the rear stage was made from wood and was then replaced by a steel construction. However, the problem with this was that it left insufficient space when trying to pull away scenery or the cyclorama.
For this reason, the theatre had long dreamed of increasing the height. During the current rebuild, we were able to realise their request, and the entire grid deck was shifted upwards by several metres.
On the main stage, the grid deck was located under the roof dome construction, and it was always necessary to climb over the girders of the dome construction. If you wanted to reposition point hoists, these always had to be lifted via the girders.
Here, too, the grating was shifted higher, and a rail system was installed for the point hoists. It is now possible to move these into position very easily, meaning that one person can do the job without major effort.
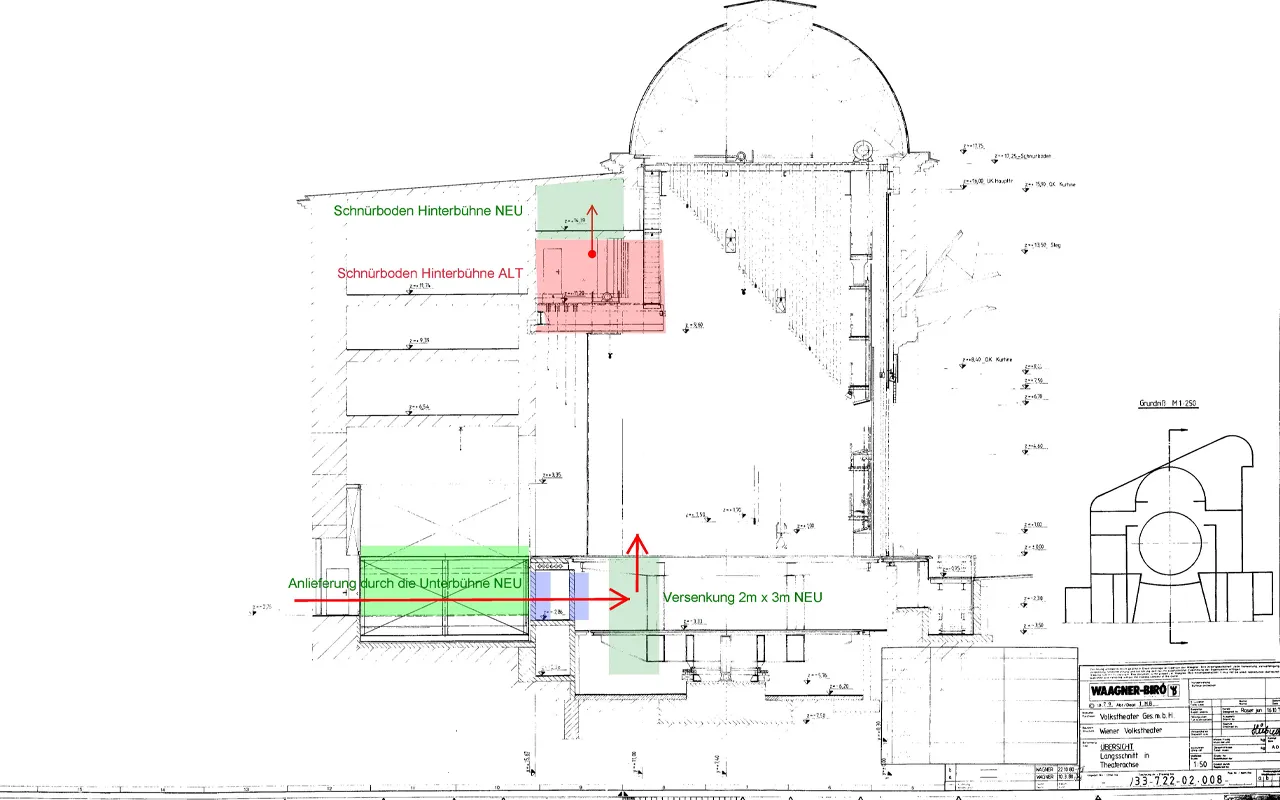
The grid decks on the rear and main stage were each lifted higher. Through the installation of passages and the enlargement of a platform in the revolving stage, it is possible to go directly into the lower stage from the street.
Control system
The theatre had already been equipped with our C⋅A⋅T V4 control system. However, the existing system was very small. All the flybars which had previously been moved manually using counterweights were now replaced by mechanical hoists. The entire stage technology (upper and below-stage machinery) was integrated into our new C⋅A⋅T V5 control system. Due to the Corona epidemic, our two-day training was done virtually at first. This worked out remarkably well. We then held another 2-day training on-site in the theatre itself, where the participants were able to try everything out live. Within this short time, the responsible operators were quickly able to familiarise themselves with our control system, as it is highly intuitive and simple in construction.
A new delivery concept
Delivery via the lower an side stages
The concept for deliveries to the theatre was completely revised and improved. It is now possible to enter the lower stage directly from the street. An existing platform in the revolving stage was enlarged so that scenery can now also be transported directly onto the main stage. In addition, a new side stage with a delivery platform was created by breaking through the outside wall. It is now possible to get onto the new side stage directly from the street.
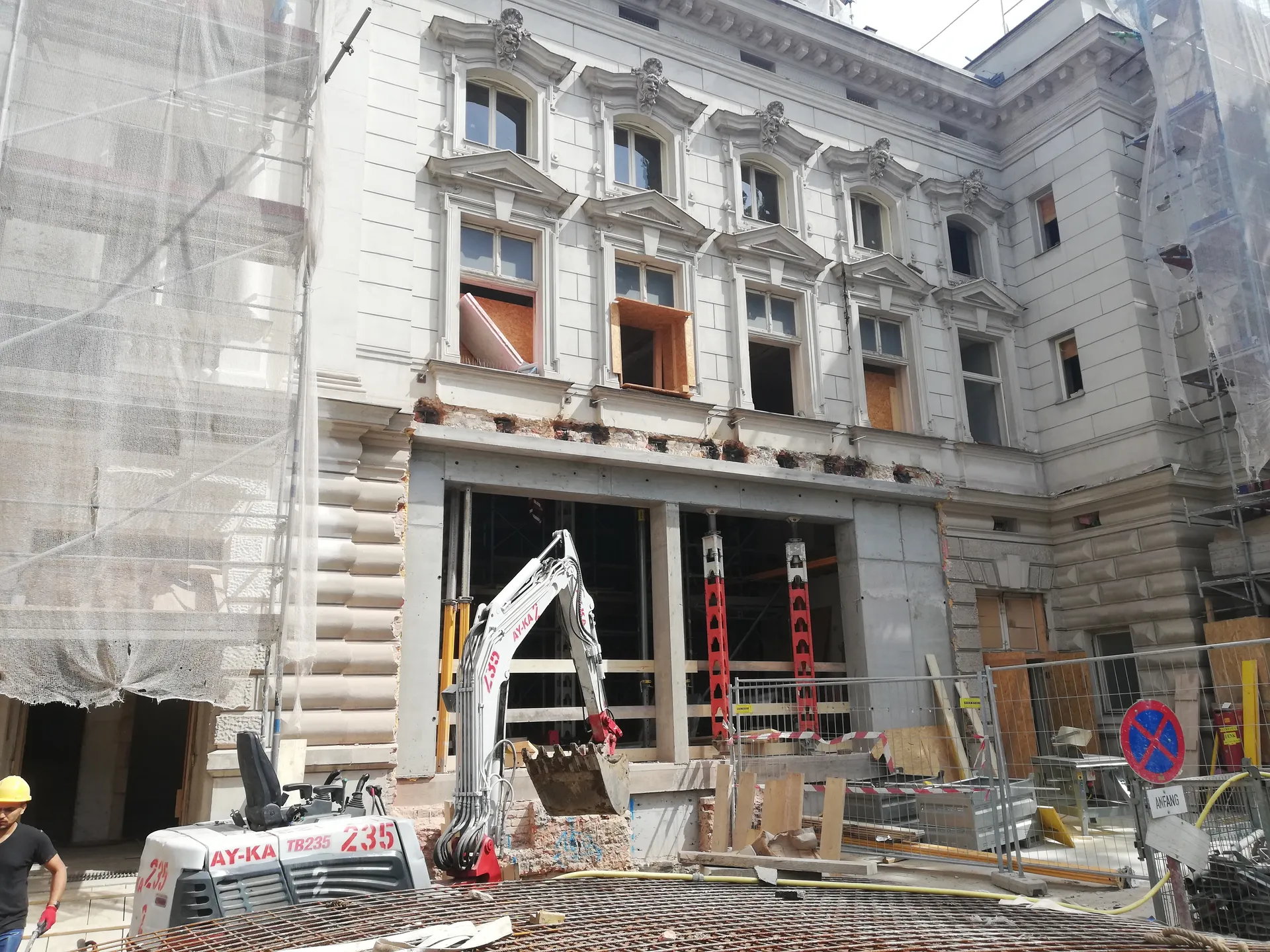
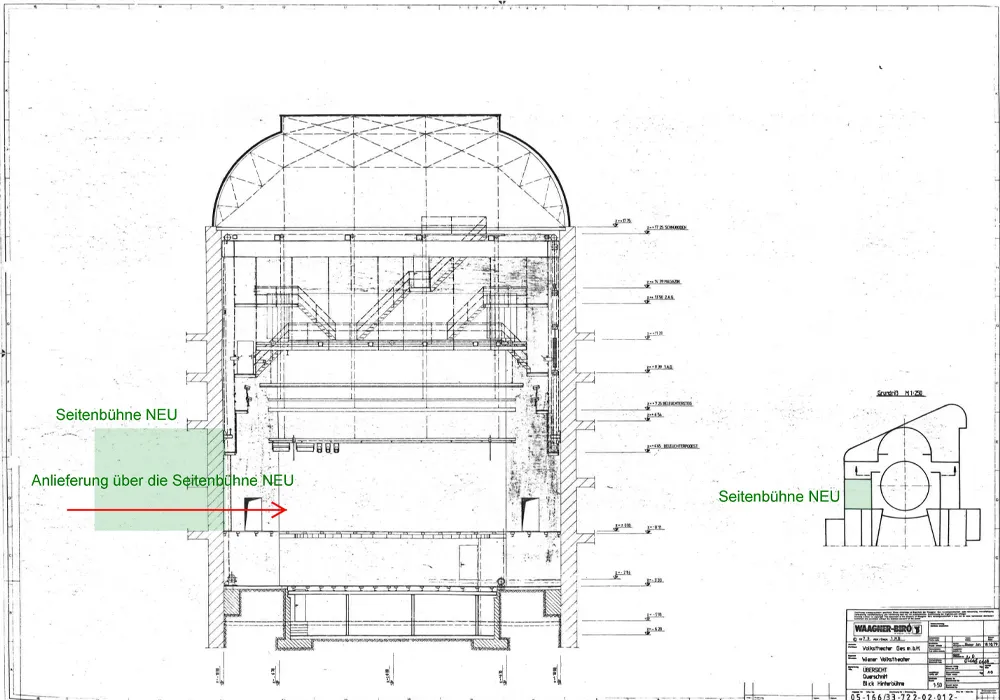
All improvements at a glance Delivery of objects via the rear stage New side stage with transport platform More lift height in the rear stage All drives (existing and new) are integrated into the C⋅A⋅T V5 control system. 3 pcs C⋅A⋅T 562 with double screen and 1 pc C⋅A⋅T 530 are used as control consoles Everything is powered by electricity Accesses to the gallery have been improved Ascents/stairs on the gallery have been replaced There is more overall space on the stage Increased safety for actors and employees
One extremely important aspect in theatres is the safety of employees and actors. How can this be guaranteed?
Yes, safety is a central topic. After all, several tonnes of scenery are frequently suspended above actors on the stage. There is no monitoring system on manual drives. The responsibility lies with the operator, and if they make a mistake, there is nothing they can do about it. There’s no emergency OFF switch or anything like that.
Our control systems, on the other hand, feature countless monitoring functions which facilitate operation. The system queries regularly whether there are any problems and alerts you faster accordingly. The overall response times of the control system are, amongst other things, much faster than those on the C⋅A⋅T V4 predecessor version.
What is particularly important when such a project is being organised?
What I noticed again during this project is that it is very important to remain in contact with the customer. This is especially when the schedule is tight. We held weekly coordination meetings regarding the construction progress with the local site management, and we addressed any issues openly. No project runs completely smoothly, and you simply have to remain solution-orientated and honest with each other. This honesty is also highly valued by the customers. And if there is a problem on our part, then we put everything in motion in order to solve it.
The regular contact with our customers doesn’t stop after we have handed over the system. This is also the case with the Volkstheater, we increasingly frequently arrange one year of real-time operation and regular user meetings.
This means that the user meetings take place bi-monthly. Lively exchanges are conducted between Waagner-Biro System Systems and the Volkstheater personnel. For example, we discuss any faults which have occurred, things which have functioned well, or possibilities for improvement. This of course provides benefits for both parties: our customers receive rapid solutions and assistance, and we can further develop control systems and planning based directly on everyday working life.
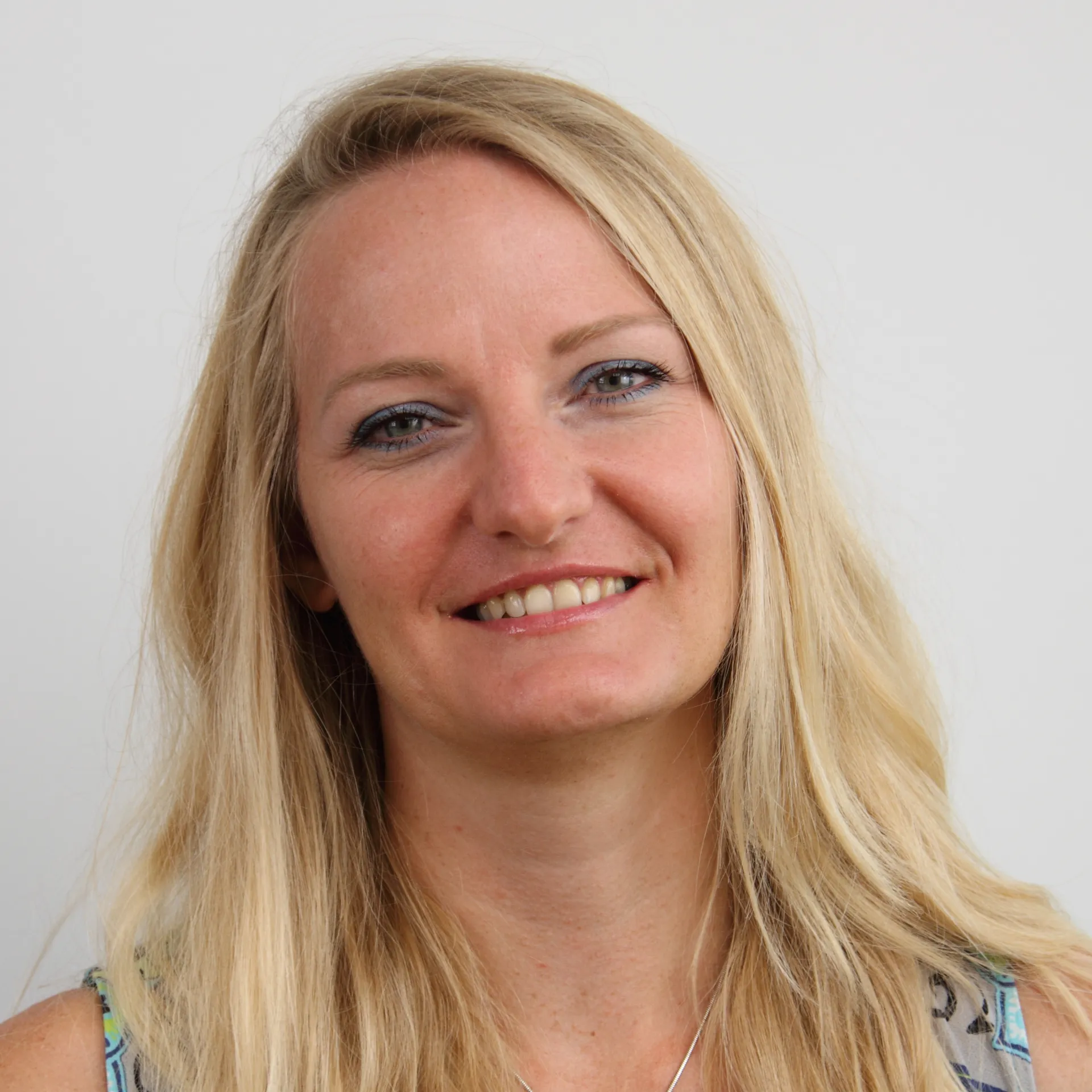
Ines Schwabl
Author
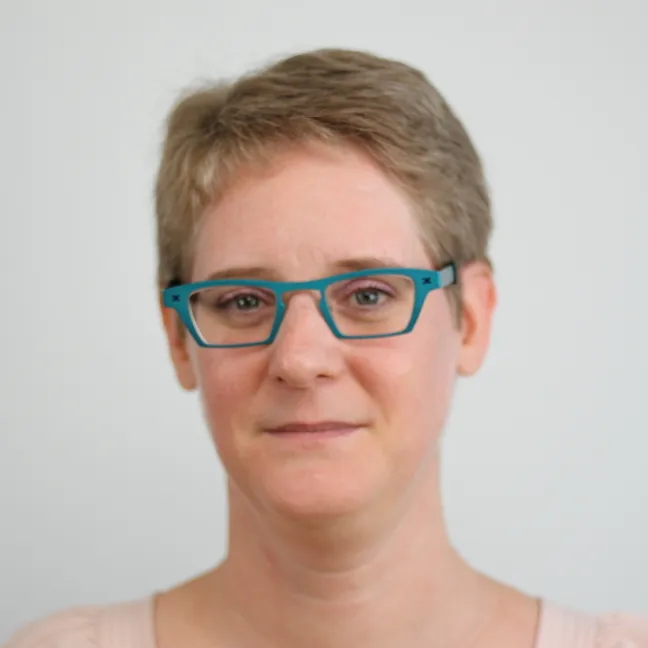
Angelika Albert-Knaus
Author
7/29/2024
In this article
Waagner Biro Stage Systems