product
C⋅A⋅T 550 & C⋅A⋅T GALLERY – two new developments for a large customer request
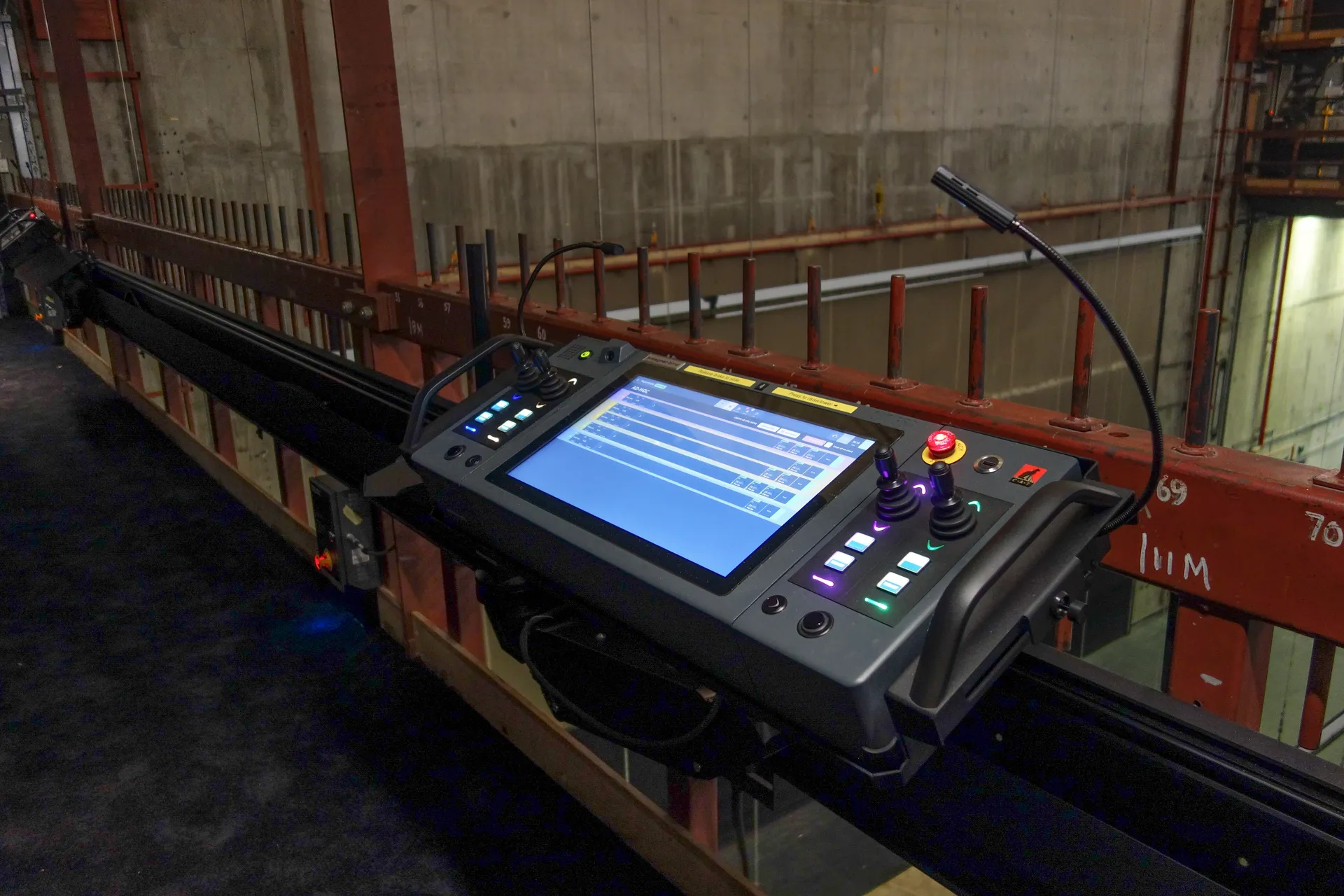
C⋅A⋅T 550
Each stage has its own specific requirements. Sometimes that calls for new ideas, just like the Arts Centre in Melbourne.
Lesezeit: 5 min 33 sec
Read the full story here about the specially developed gallery console system for the State Theatre in the Arts Centre in Melbourne.
Our brand-new C⋅A⋅T V5 control console was first presented to the team and to the technical director of the Arts Centre Melbourne during the product launch in 2017 at the Stage Set Scenery trade fair in Berlin. Besides very promising feedback on the software and the control concept, there was, however, one major concern that would have made all the ideas and concepts implemented in the software moot: the dimensions of our C⋅A⋅T 562 main control console seemed too large for the available space in the gallery of the State Theatre in the Arts Centre Melbourne.
Challenges drive innovation!
Traditional approaches, such as mounting a C⋅A⋅T 530 mobile console on the gallery of the State Theatre, could not meet the requirements of a high-performance main control console with a 3D interface, not least because of the insufficient size of the displays and the restriction to 2 possible control levers. On the contrary, the new development was to be equipped with ergonomically operable screens and four control levers, thereby combining the overall performance of C⋅A⋅T V5 in a smaller housing with a lower overall installation depth. At the same time, the new console was to offer maximum flexibility in terms of handling in the gallery, so that the operators did not impair one another when working in the narrow passages of the gallery and so that they always experience the best combination of ergonomic operation and a view of the happenings onstage.
One seamless operation: from prototype to C⋅A⋅T GALLERY System
After trialling many approaches to meet all these requirements, we developed a new console and a support arm that can be flexibly adjusted in all necessary axes.
Our colleague Christoph is a hardware developer at WB Luxembourg and was involved in the gallery console project for the ACM Melbourne from the very start. In an interview, Christoph told us about this exciting product development.
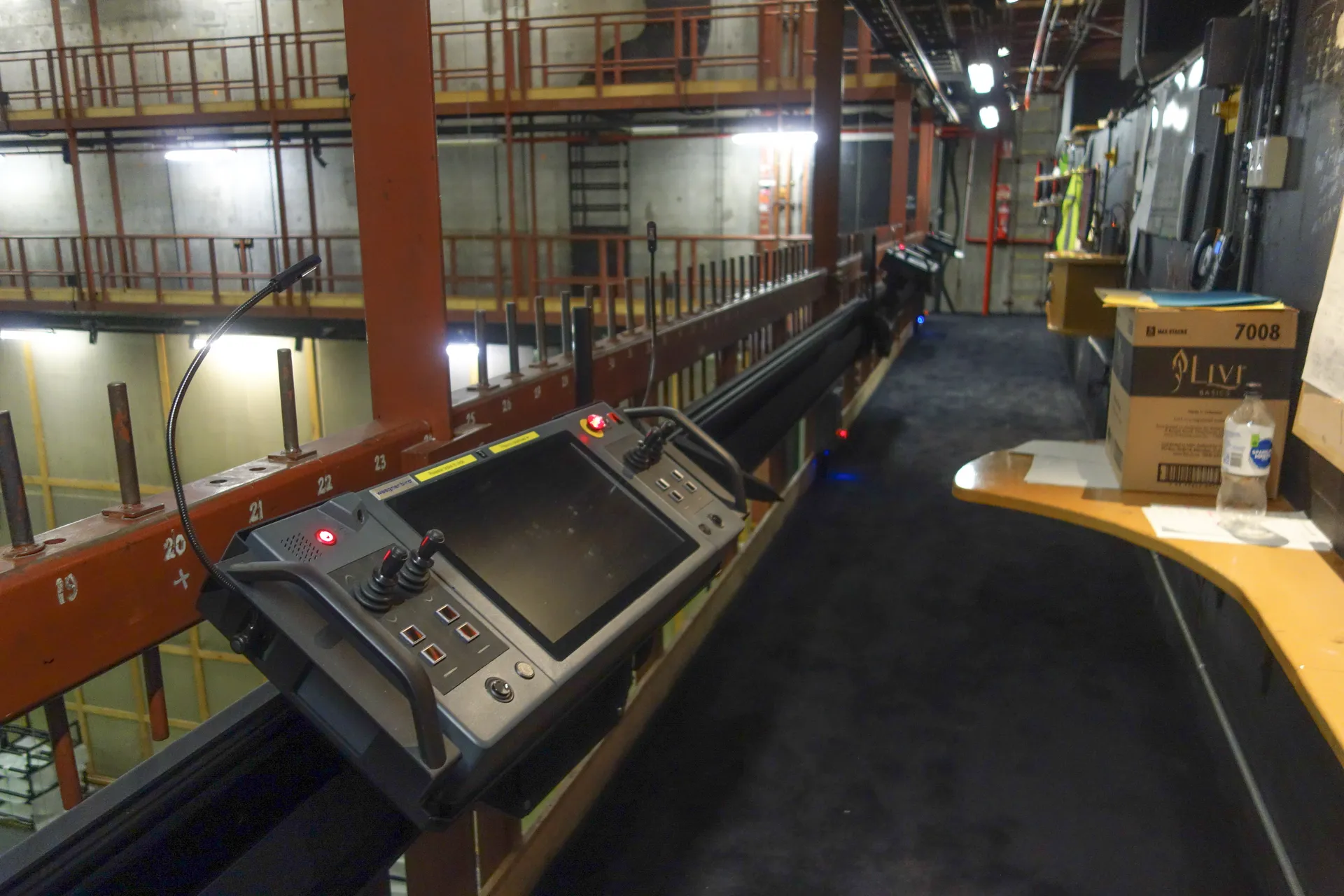
Installed C⋅A⋅T GALLERY
Christoph, what was your vision for this development?
The goal was to design a compact, slender console. The operator had to have a high-performance operator console but not be restricted during operation by the size of the device. The basic idea was to deliver the performance of a C⋅A⋅T 560 or C⋅A⋅T 562 but the dimensions of the console should be only slightly bigger than those of the C⋅A⋅T 530. In addition, the console needed to be integrated seamlessly with the C⋅A⋅T GALLERY track, which was also in development.
Who was involved in this development?
My boss, Jean-Marie Schiltz, in the Luxembourg development team, an external product design team and an internal and external construction team took part in the development. As product manager, Jean-Marie always delivered the best ideas for our team and drew up sophisticated concepts. So right from the start, it was Jean-Marie who took care of the entire development process for the gallery consoles and stands, and also ensured that schedules were adhered to. The external product design team was already familiar with the C⋅A⋅T V5 product line so they could make quick progress with the design. The Vienna construction team prepared the blueprint for the mechanical construction, external design engineers and technicians drafted the construction in 2D drawings and at the same time prepared the production documents. Technical alterations were also discussed together, which allowed us to get started with production quickly.
I took care of and coordinated the electrics and electronics for the console types. When bringing a product onto the market, it is also very important that you keep supply chain management in mind and act promptly when problems arise.
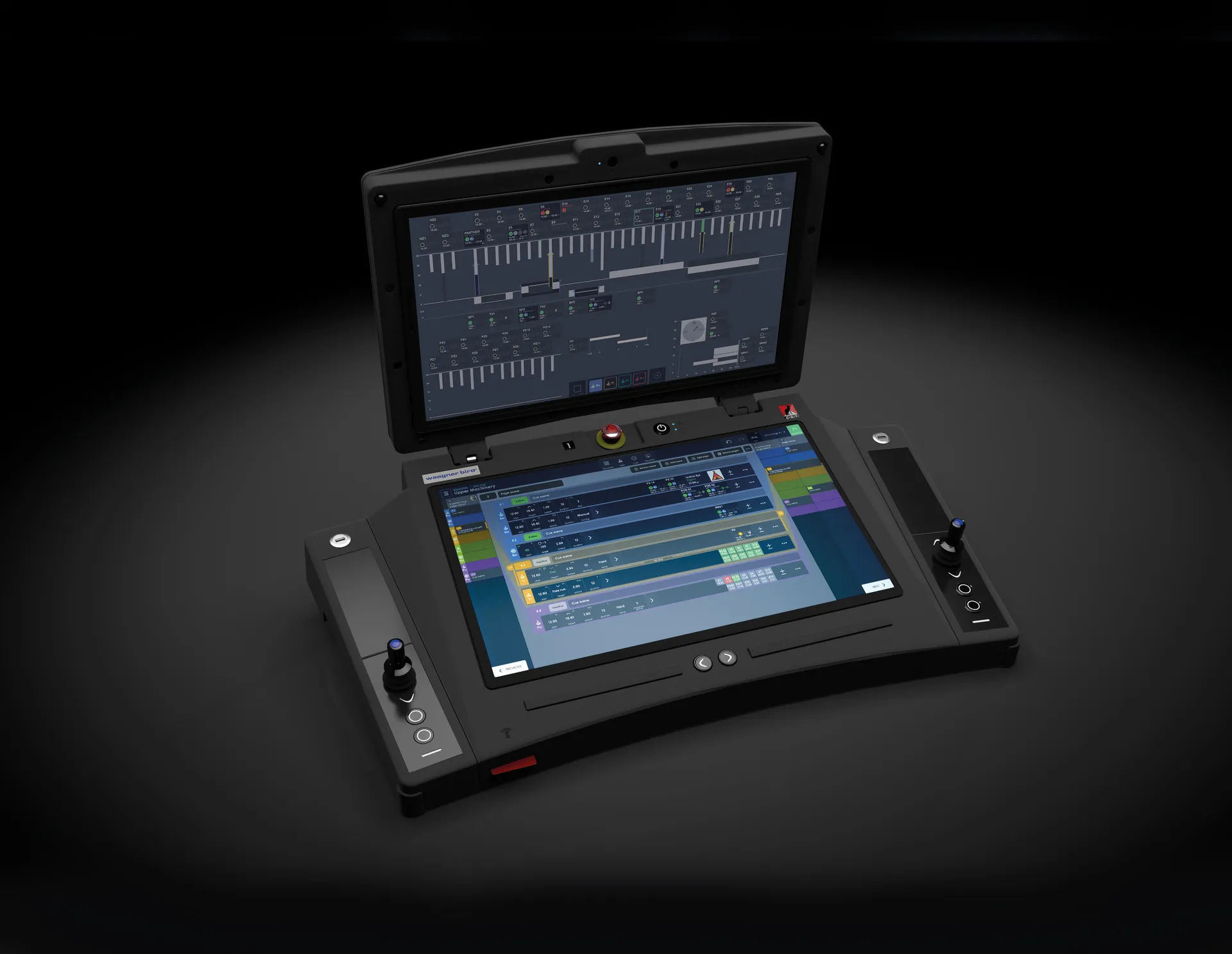

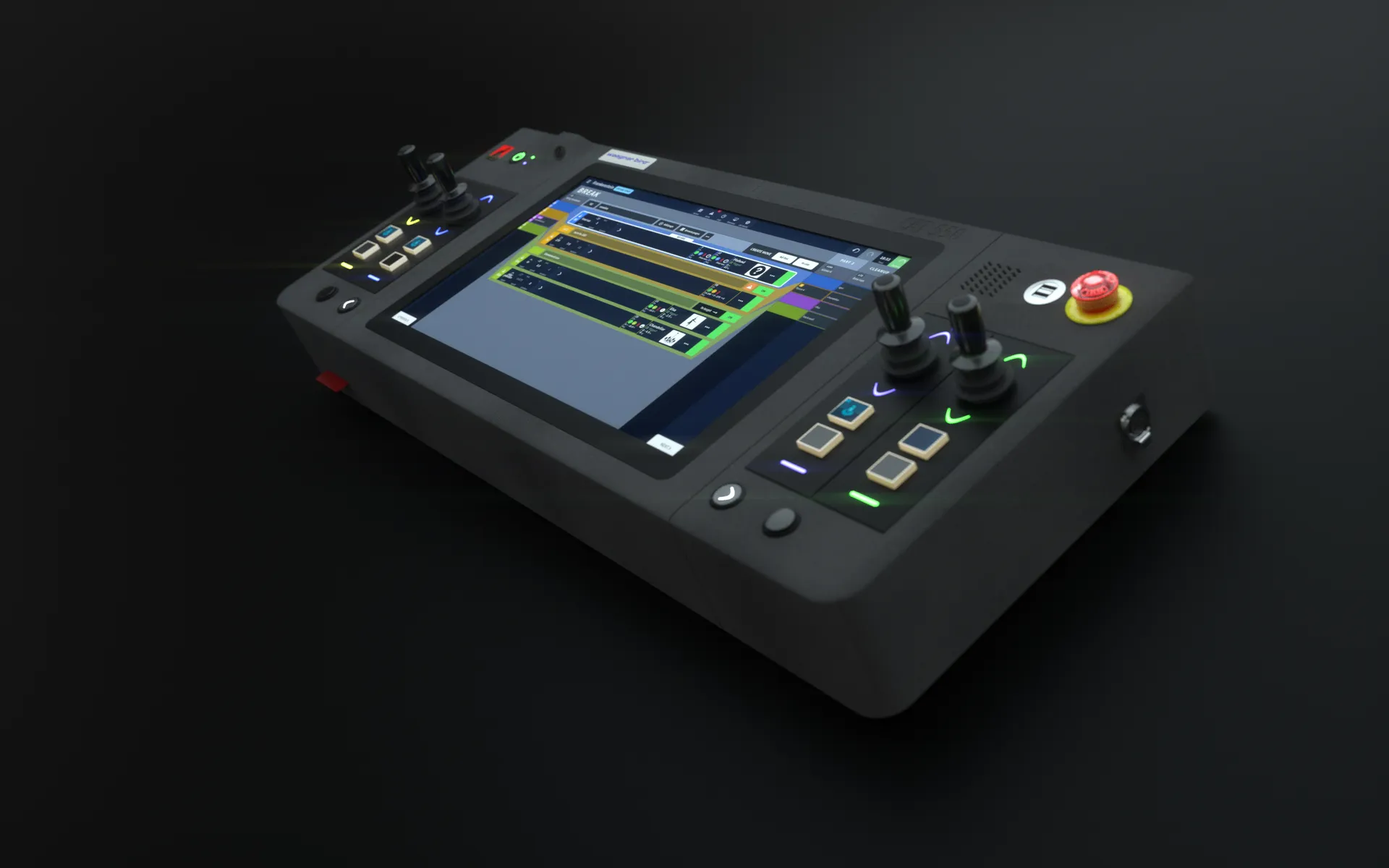
Photo left: C⋅A⋅T 562 / Photo centre: C⋅A⋅T 530 / Photo right: new gallery desk C⋅A⋅T 550
Christoph, can you give us some examples of the coordination needed for such a project?
We always tried to accommodate our customer and meet the deadlines. It was very important to observe how the process was developing and how the development (in terms of phases) was progressing. It was just as important to pay attention to the commercial specifications, as our development costs had to remain within the budget, in the same way as series production. As a result, I maintained a constant presence in several project work groups, which met several times per week and discussed the progress made and, of course, any problems that arose. Jean-Marie was always closely involved and together we discussed the next catalogue of measures, which were then communicated to the individual teams/work groups.
And how do you motivate yourself to keep moving forward?
Bringing a product to market generates a great deal of joy. This joy motivates me and makes me very proud. As with all our products, the solutions for the intended user experience simply must fit! This is where the expertise of our longstanding partners in construction and design also plays an important role. Our partners guarantee that the 3D models we have developed will be produced perfectly every time. They accompany the development completely up to the productive use. We want to maximize the benefit to the customer!
At this point, the C⋅A⋅T service also comes into play. After all, we provide the customer with the perfect system according to our motto: “Well, if it was easy, ANYONE could do it.” Results like this make me very proud and bring fresh motivation to our teams and me every day.
Is there a moment that is particularly memorable to you?
Initially, we had just a couple of drafts for the device, sketched out on paper. In terms of hardware, things moved quickly. After two prototypes we were already in a position to bring the product to market. Fitting the screen was particularly difficult. We needed to integrate a 19.5” touchscreen into the much smaller console. At that point, I was concerned about how the aluminium construction would be manufactured. But this also turned out really well.
How do you (yourself/the team) feel now when the product (your baby) is finally installed and functioning?
I just feel really happy. The motivation that comes from this inspires me to develop more ideas and concepts. Each new development task makes you “hungrier”! Put simply, you always want to develop new products, be successful and celebrate yet another successful project.
And what does our customer say about their new C⋅A⋅T Gallery Console System?
Waagner-Biro Stage Systems in an interview with Chris King (Managing Director) and David Harvey (Technical Director) of the Melbourne Arts Centre.
Chris, ultimately, what was the crucial factor in commissioning Waagner Biro Stage Systems with the renovation of the State Theatre?
Today, Waagner Biro Stage Systems is one of the most experienced and respected companies for stage automation anywhere in the world. The broad spectrum of experience and support that was continually offered to the Arts Centre Melbourne made the bid from Waagner Biro Stage Systems very compelling. However, the crucial factor was the ability of Waagner Biro Stage Systems to address our wishes and develop the new gallery console that would serve our purposes and meet our requirements.
What was your first impression when you saw the newly developed C⋅A⋅T gallery console at a 1:1 scale at the control system presentation in 2017?
Chris: My first impression was: “What an elegant and compact solution! How did Waagner Biro Stage Systems manage to put it together so quickly?”
David: What struck me most of all was that Waagner Biro Stage Systems had understood the spatial problem that we have on our fly galleries perfectly and had designed the new C⋅A⋅T 550 console so that it met all our specific and operational requirements.
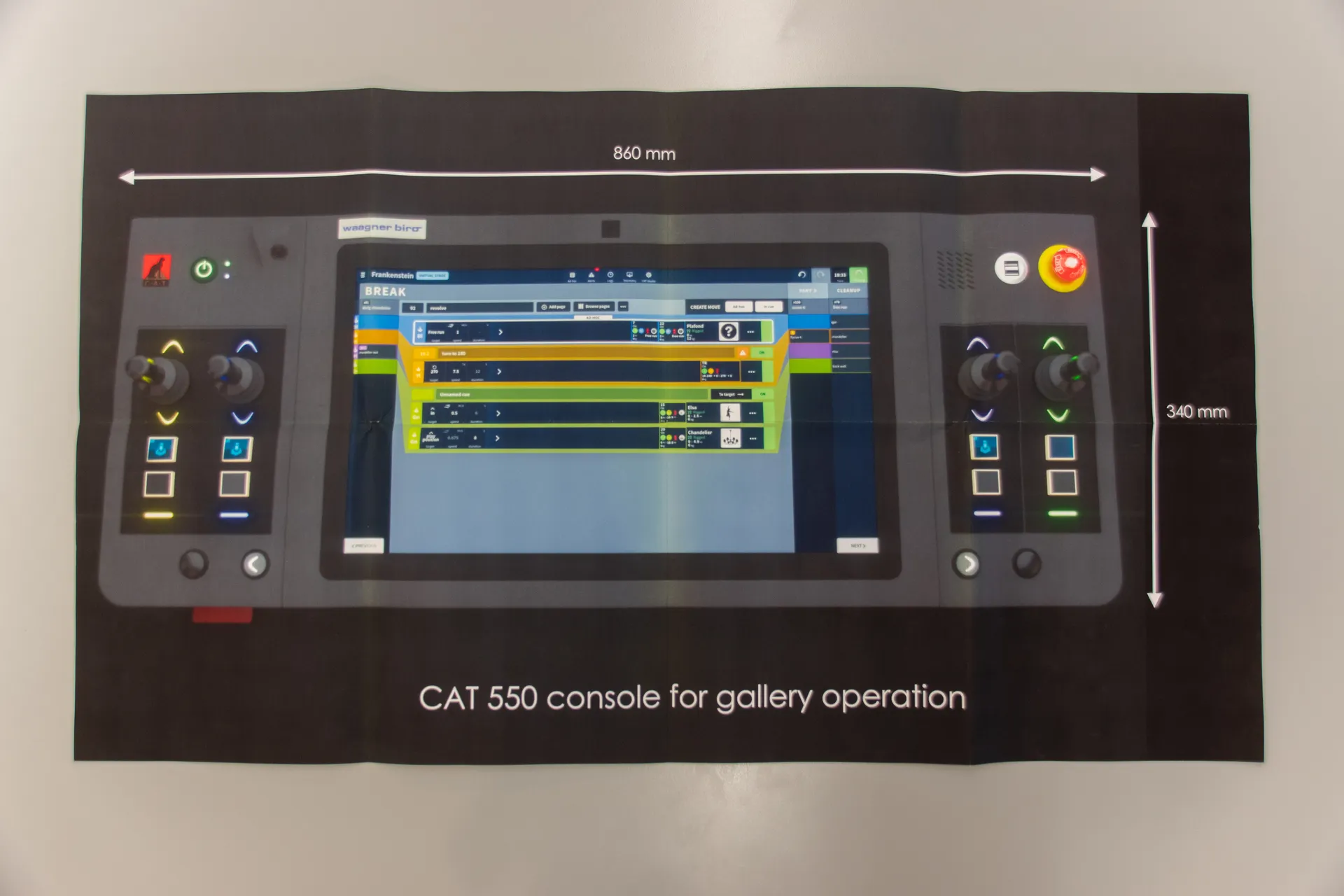
Printout in original size
What was the particular challenge that you were confronted with and that ultimately led to the development of the new C⋅A⋅T 550 console?
Chris & David: The State Theatre in Melbourne has some restrictions that mean we are unable to extend the stagehouse or the auditorium. In our planning for the new automation system, we had to stipulate clear restrictions and one of these is the operator station. The fly gallery operator station is very narrow, so any console placed there had to fit into these restrictions and limitations. Furthermore, the State Theatre also works on the principle that the operator always has a sightline to the moving object. So, it was important for us to ensure that the control console could move as close as possible to the moving rail.
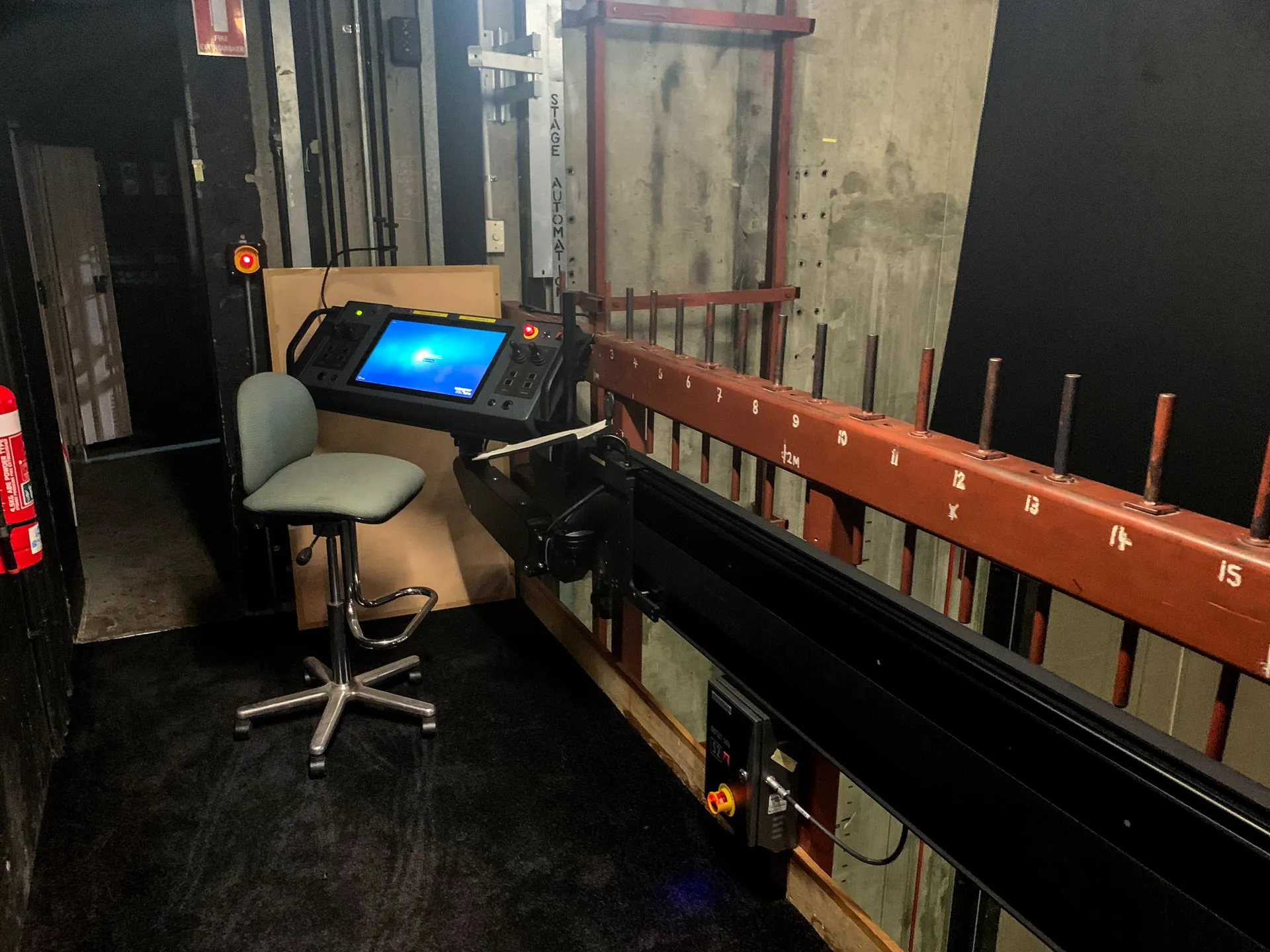
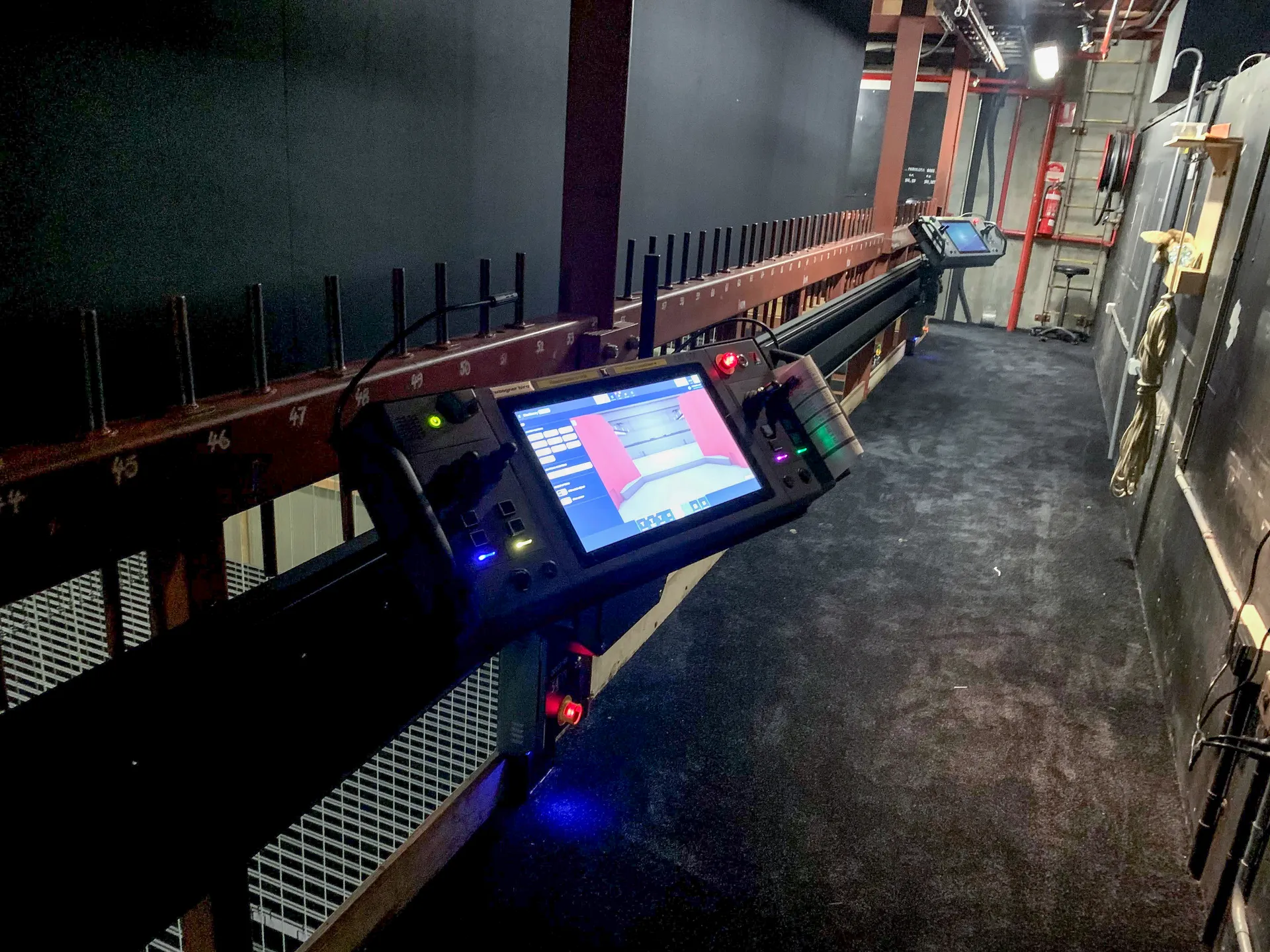
Operator stations in the Fly Gallery
Chris, can you remember the feedback you gave to our colleagues during this presentation in 2017?
Chris: I remember clearly how good it was that Waagner Biro Stage Systems had listened to our requirements, had taken the time to understand sour situation and help us with a solution to the problem.
What was your reaction when you heard that the finished new development of the C⋅A⋅T 550 was based on your input?
Chris: I was very pleased. It is always great to know that a company can really listen and understand the needs of a customer – and then find a way to meet these.
David: I can only echo what Chris has said.
New Control System CAT 550 at Arts Center Melbourne
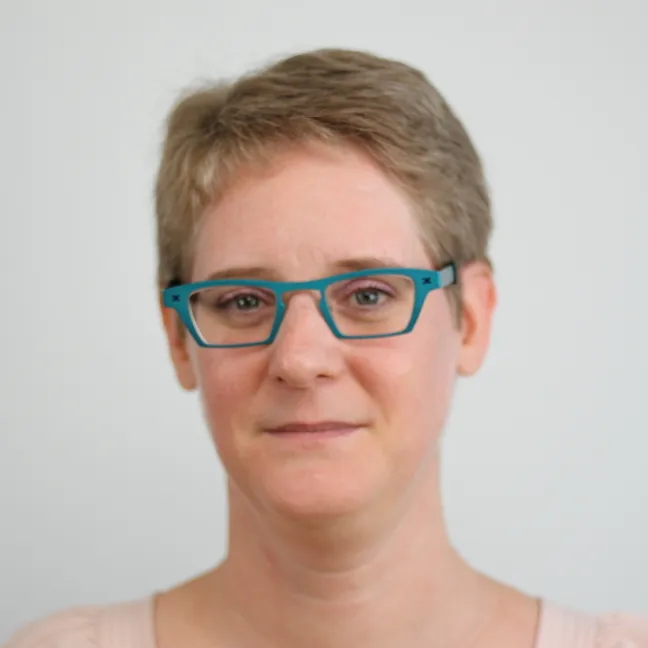
Angelika Albert-Knaus
Author
7/31/2024
In this article
Waagner Biro Stage Systems